Pharmaceutical

Use cases: Training, Line Change-Overs, Evaluations
Problem
When Galderma contacted DeepSight they were struggling to keep their production line running at maximum capacity.
Workers on the night and weekend shifts were unable to correctly perform the required changeovers which resulted in delays and detrimental equipment breakdowns.
In order to maximize the uptime of the machines across the factory, Galderma knew they needed a new solution that would transfer the knowledge the operators needed and also give them a way to connect with remote support specialists.
Solution
With our help, Galderma implemented 3-D virtual guides, giving operators 24/7 access to machine operations knowledge. Workers are not only able to easily familiarize themselves with the location of the different adjustors, but can also practice virtually while the machines are operating to improve their skills.
They have successfully used DeepSight’s platform to optimize three production lines and are gradually adding more.
When a problem cannot be resolved with the 3-D guides, operators are able to remotely connect with specialized technicians without halting production.
- 3D instructions
- Knowledge Capture
- Skills Management
With DeepSight, it’s as if we finally had a multitude of expert employees to help us integrate our new employees.
— Richard Sefler, Chief Operational Excellence and training
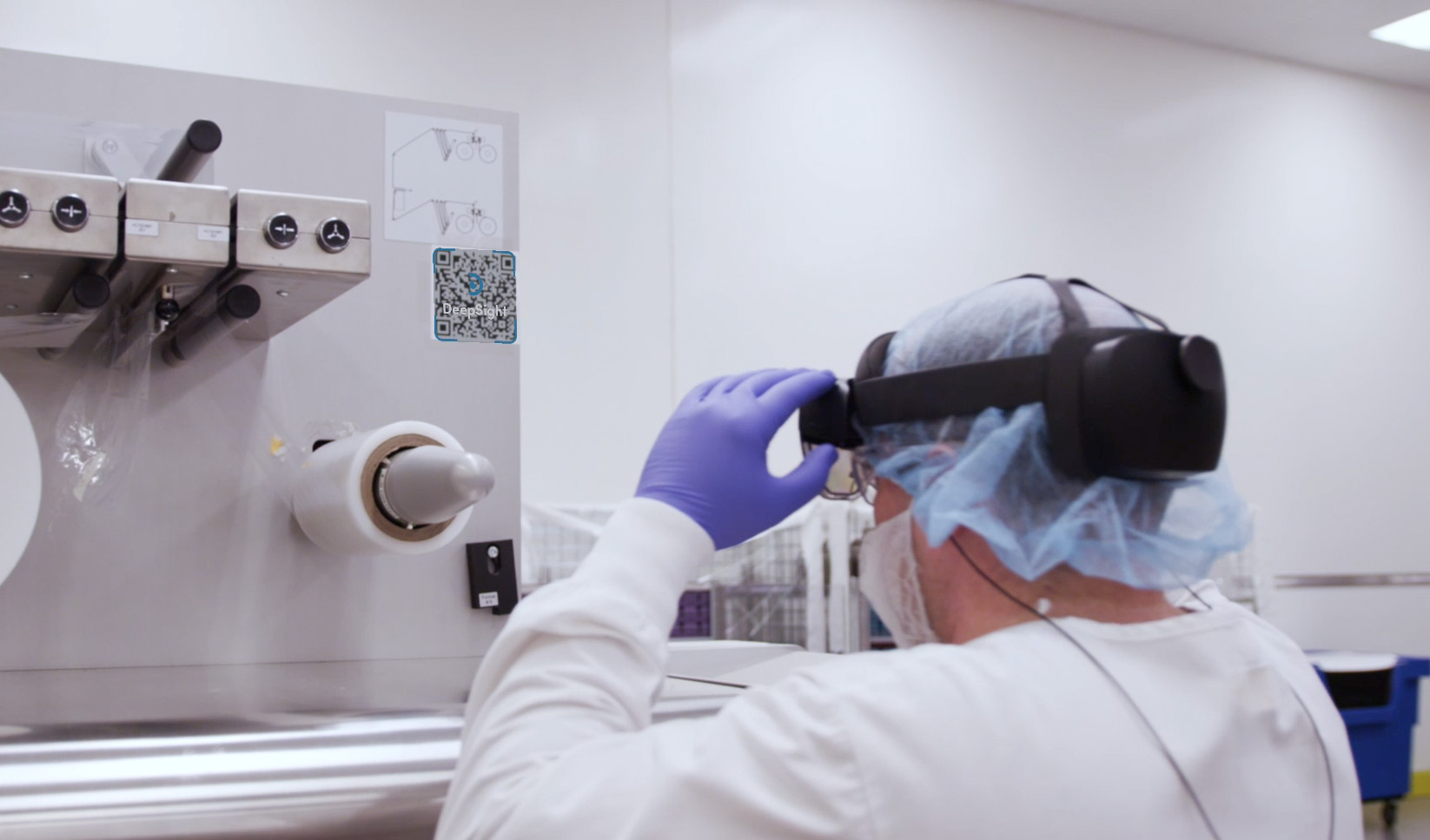